在现代精密制造与高精度测量设备中,花岗岩构件因其优异的物理特性和稳定的结构性能,广泛应用于机床底座、三坐标测量仪平台、CNC设备基础等关键部位。其中,抗振性能是衡量花岗岩构件质量与适用性的重要指标之一,直接影响设备运行的稳定性与测量精度。
花岗岩是一种天然的火成岩,具有致密的晶体结构和较高的硬度。其内部晶粒排列紧密,内阻尼性能优于金属材料,因此具备良好的吸振与减振能力。相比于铸铁或钢材,花岗岩构件在受到外界振动激励时,能够更快地吸收并衰减振动能量,从而减少对精密设备的干扰。这一特性使其在需要高稳定性的环境中具有显著优势,如光学测量仪器、半导体制造设备等。
尽管花岗岩本身具备良好的抗振性能,但其实际应用效果还与结构设计密切相关。合理的结构优化可以进一步提升其动态响应能力。例如,在大型花岗岩底座的设计中,采用加强筋结构、蜂窝状空腔布局等方式,可以在不增加重量的前提下提高整体刚度,并有效分散应力集中区域,降低共振风险。
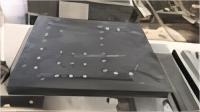
此外,现代设计中越来越多地引入有限元分析(FEA)技术,对构件进行模态分析与动态仿真,以预测其在不同频率下的振动响应。通过模拟不同结构形式的振动特性,工程师可优化几何形状、支撑位置及连接方式,从而实现较佳的抗振效果。
值得注意的是,安装方式也对其抗振性能有重要影响。采用弹性支撑垫块或主动隔振系统,能有效隔离外部振动源,进一步提升系统的稳定性。同时,在加工过程中应尽量减少残余应力的产生,避免因内部应力释放而导致的变形或裂纹扩展。
综上所述,花岗岩构件凭借其较好的天然抗振性能,在精密设备中扮演着关键的角色。而通过科学的结构优化设计与先进的仿真技术手段,可以进一步挖掘其潜力,提升整体设备的动态稳定性与工作精度。未来,随着智能制造与超精密加工技术的发展,花岗岩构件的抗振性能研究与结构优化设计将继续成为行业关注的重点方向。